导读相信目前很多小伙伴对于模具设计流程都比较感兴趣 , 那么小搜今天在网上也是收集了一些与模具设计流程相关的信息来分享给大家 , 希望能够帮助...
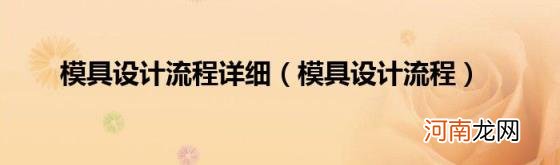
文章插图
相信目前很多小伙伴对于模具设计流程都比较感兴趣 , 那么小搜今天在网上也是收集了一些与模具设计流程相关的信息来分享给大家 , 希望能够帮助到大家哦 。
第一步:对制品2D图及3D图的分析和消化 , 其内容包括以下几个方面:1、制品的几何形状 。2、制品的尺寸、公差及设计基准 。3、制品的技术要求(即技术条件) 。4、制品所用塑料名称、缩水及颜色 。5、制品的表面要求 。第二部:注射剂型号的确定注射剂规格的确定主要是根据塑料制品的大小及生产批量 。设设计人员在选择注射机时 , 主要考虑其塑化率、注射量、锁模力、安装模具的有效面积(注射机拉杆内间距)、容模量、顶顶出形式及定出长度 。倘若客户已提供所用注射剂的型号或规格 , 设计人员必须对其参数进行校核 , 若满足不了要求 , 则必须与客户商量更换 。第三部:型腔数量的确定及型腔排列模具型腔数量的确定主要是根据制品的投影面积、几何形状(有无侧抽芯)、制品精度、批量以及经济效益来确定 。型腔数量主要依据以下因素进行确定:1、制品的生产批量(月批量或年批量) 。2、制品有无侧抽芯及其处理方法 。3、模具外形尺寸与注射剂安装模具的有效面积(或注射机拉杆内间距) 。4、制品重量与注射机的注射量 。5、制品的投影面积与锁模力 。6、制品精度 。7、制品颜色 。8、经济效益(每套模的生产值) 。以上这些因素有时是相互制约的 , 因此在确定设计方案时 , 必须进行协调 , 以保证满足其主要条件 。性强数量确定之后 , 便进行型腔的排列 , 以及型腔位置的布局 。型腔的排列涉及模具尺寸、浇注系统的设计、浇注系统的平衡、抽芯(滑块)机构的设计、镶件型芯的设计以及热流道系统的设计 。以上这些问题由于分型面及浇口位置的选择有关 , 所以在具体设计过程中 , 要进行必要的调整 , 以达到最完美的设计 。第四步:分型面的确定分型面 , 在一些国外的制品图中已作具体规定 , 但在很多的模具设计中要由模具人员来确定 , 一般来讲 , 在平面上的分型面比较容易处理 , 有时碰到立体形式的分型面就应当特别注意 。其分型面的选择应遵照以下原则:1、不影响制品的外观 , 尤其是对外观有明确要求的制品 , 更应注意分型面对外观的影响 。2、利于保证制品的精度 。3,、利于模具加工 , 特别是型腔的加工 。先复机构 。4、利于浇注系统、排气系统、冷却系统的设计 。5、利于制品的脱模 , 确保在开模时使制品留于动模一侧 。6、便于金属嵌件 。在设计侧向分型机构时 , 应确保其安全可靠 , 尽量避免与定出机构发生干扰 , 否则在模具上应设置先复机构 。第六步:模架的确定和标准件的选用以上内容全部确定之后 , 便根据所定内容设计模架 。在设计模架时 , 尽可能地选用便准模架 , 确定出标准模架的形式、规格及A、B板厚度 。标准件包括通用标准件及模具专用标准件两大类 。通用标准件如紧固件等 。模具专用标准件如定位圈、浇口套、推杆、推管、导柱、导套、模具专用弹簧、冷却及加热元件、二次分型机构及精密定位用标准组件等 。需要强调的是 , 设计模具时 , 尽可能地选用标准模架和标准件 , 因为标准件有很大一部分已经商品化 , 随时可以在市场上买到 , 这对缩短制造周期、降低制造成本是极其有利的 。买家尺寸确定之后 , 对模具有关零件要进行必要的强度和刚性计算 , 以校核所选模架是否适当 , 尤其是对大型模具 , 这一点尤为重要 。第七步:浇注系统的设计浇注系统的设计包括主流道的选择、分流道截面形状及尺寸的确定 。如采用点浇口时 , 为确保分流道的脱落 , 还应注意脱浇口装置的设计 。在设计浇注系统是 , 首先是选择浇口的位置 。浇浇口位置选择的适当与否 , 将直接关系到制品成型质量及注射过程是否能顺利进行 , 浇口位置的选择应遵循以下原则:1、浇口位置应尽量选择在分型面上 , 以便于模具加工及使用浇口的清理 。2、浇浇口位置距型腔各个部位的距离应尽量一致 , 并使其流程为最短(一般大水口很难做到) 。3、浇口位置应保证塑料注入型腔时对着型腔中宽敞、厚壁部位 , 以便于塑料流入 。4、避免塑料在流入型腔时直冲到型腔壁、型芯或嵌件 , 是塑料能尽快流入型腔各部位 , 并避免型芯或嵌件变形 。5、尽量避免制品产生熔接痕 , 若要产生 , 使其溶解痕产生在制品不重要的地方 。6、浇口位置及其塑料注入方向 , 应是塑料在注入型腔时能沿着型腔平行方向均匀地流入 , 并有利于型腔内气体的排出 。7、浇口应设计在制品上最容易清除的部位 , 同时尽可能不影响制品的外观 。第八步:顶出系统的设计制品的顶出形式 , 归纳起来可分为机械顶出、液压顶出、气动顶出三大类 。在机械顶出是注射成型过程中最后一个环节 , 顶出质量的好坏将最后决定制品的质量 , 因此 , 制品顶出是不可忽视 。在设计顶出系统时应遵守下列原则:1、为使制品不致因顶出产生变形 , 推力点应尽量靠近型芯或难于脱模的部位 , 如制品上细长的中空圆柱 , 多采用推管顶出 。推力点的布置应尽量平衡 。2、推力点应作用在制品能承受力最大的部位 , 及刚性好的部位 , 如筋部、突缘、壳体型制品的壁缘等处 。3、尽量避免推力点作用在制品较薄平面上 , 防止制品顶白、顶高等 , 如壳体形制品及筒形制品多采用推板顶出 。4、尽量避免顶出痕迹影响制品外观 , 顶出装置应设在制品的隐蔽面或非装饰表面 。于透明制品尤其要注意定出位置及顶出形式的选择 。5、为使制品在顶出时受力均匀 , 同时避免因真空吸附而使制品产生变形 , 往往采用复合顶出或特殊形式的顶出系统 , 如推杆、推板或推杆、推管复合顶出 , 或者采用进气事推杆、推块等定出装置 , 必要时还应设置进气阀 。第九步:冷却系统的设计冷却系统的设计是一项较繁琐的工作 , 要考虑冷却效果、冷却的均匀性和冷却系统对模具整体结构的影响 。冷却系统的设计包括以下内容:1、冷却系统的排列方式及冷却系统的具体形式 。2、冷却系统的具体位置及尺寸的确定 。3、重点部位如动模型芯或镶件的冷却 。4、侧滑块及侧滑芯的冷却 。5、冷却元件的设计及冷却标准元件的选用 。6、密封结构的设计 。第十步:塑料注射模上的导向装置 , 在采用标准模架时 , 已经确定下来 。一般情况下 , 设计人员只要按模架规格选用就可以了 。但根据制品要求须设置精密导向装置时 , 则必须由设计人员根据模具结构进行具体设计 。一般导向分为:动、定模之间的导向;推板及推杆固定板导向;推板杆与动模板之间的导向;定模座与推刘盗版之间的导向 。一般导向装置由于受加工精度的限制或使用一段时间之后 , 其配合精度降低 , 会直接影响制品的精度 , 因此对精度要求较高的制品必须另行设计精密定位元件 , 有的已经标准化 , 如锥形定位销、定位块等可供选用 , 但有些精密导向定位装置须根据模块的具体结构进行专门设计 。第十一部:模具钢材的选用模具成型零件(型腔、型芯)材料的选用 , 主要根据制品的批量、塑料类别来确定 。对对于高光泽或透明的制品 , 主要选用4Cr13等类型的马氏体耐蚀不锈钢或时效硬化钢 。含有玻璃纤维增强的塑料制品 , 则应选用Cr12MoV等类型的具有高耐磨性的淬火钢 。当制品的材料为PVC、POM或含有阻燃剂时 , 必须选用耐蚀不锈钢 。十二步:绘制配装图排位模架及相关内容确定之后 , 便可以绘制装配图 。在绘制装配图过程中 , 对已选定的浇注系统、冷却系统、抽芯系统、顶出系统等做出进一步的协调和完善 , 从结构上达到比较完美的设计 。第十三步:模具主要零件图的绘制在绘制型腔或型芯图时 , 必须主义所给定的成型尺寸、公差及脱模斜度是否相协调 , 其设计基准是否与制品的设计基准相协调 。同时还要考虑型腔、型芯在加工时的工艺性及使用时的力学性能及其可靠性 。结构件图的绘制 , 当采用标准模架时 , 出标准模架以外的结构件 , 大部分可以不绘制结构件图 。第十四步:设计图纸的校对模具图设计完成后 , 模具设计人员将设计图及相关原始资料一同交主管人员进行校对 。校对人员应针对客户所提供的有关设计依据及客户所提要求 , 对模具的总体结构、工作原理、操作的可行性等进行系统的校对 。第十五步:设计图纸的会签模具设计图纸完成之后 , 必须立即交给客户认可 。只有客户同意后 , 模具才可以备料投入生产 。当客户有较大意见需要作重大修改时 , 则必须在再重新设计后再交给客户认可 , 直至客户满意为止 。第十六步:排气系统对确保制品成型质量起着至关重要的作用 , 其排气方式有以下几种:1、利用排气槽 。排气槽一般设在型腔最后被充满的部位 。排气槽的深度因塑料不同而异 , 基本上是以塑料不产生飞边时所允许的最大间隙来确定 。2、利用型芯、镶件、推杆等的配合间隙或专用排气塞排气 。3、有时为了防止在制品在顶事造成真空变形 , 必须设计排气镶针 。结论综合以上的模具设计程序 , 其中有些内容可以合并考虑 , 有些内容则要反复你考虑 。因为其中因素常常相互矛盾 , 必须在设计过程中不断论证、相互协调才能得到较好的处理 , 特别是涉及模具结构方面的内容 , 一定要认真对待 , 往往要做几个方案同时考虑 , 对每一种结构尽可能列出各方面的优缺点 , 在逐一分析 , 进行优化 。结构上的原因会直接影响模具的制造和使用 , 后果严重点甚至会造成整套模具报废 。所以 , 模具设计是保证模具质量的关键性的一步 , 其设计过程就是一项系统工程 。
- 剑门关风景区最优路线 剑门关景区景点详细介绍
- 剧本杀主持如何走流程 剧本杀主持新手流程
- 大专直接考研究生流程 大专怎么直接升研究生
- 辩论赛规则和流程 辩论赛规则一二三四辩哪个厉害
- 第一次辟谷的详细流程 自己在家辟谷减肥的正确方法
- 店铺宝全店包邮模板如何设置?流程是什么?
- 办签证的流程 办签证的流程及时间
- 淘宝保税仓新仓招募计划是什么?详细介绍
- 1688一件代发市场准入和推出机制是什么?详细规则
- 拼多多怎样申请退订单?流程是什么?